In our unique facility, around 40 enthusiastic colleagues contribute to the energy transition and the process of making agriculture in Europe more sustainable.
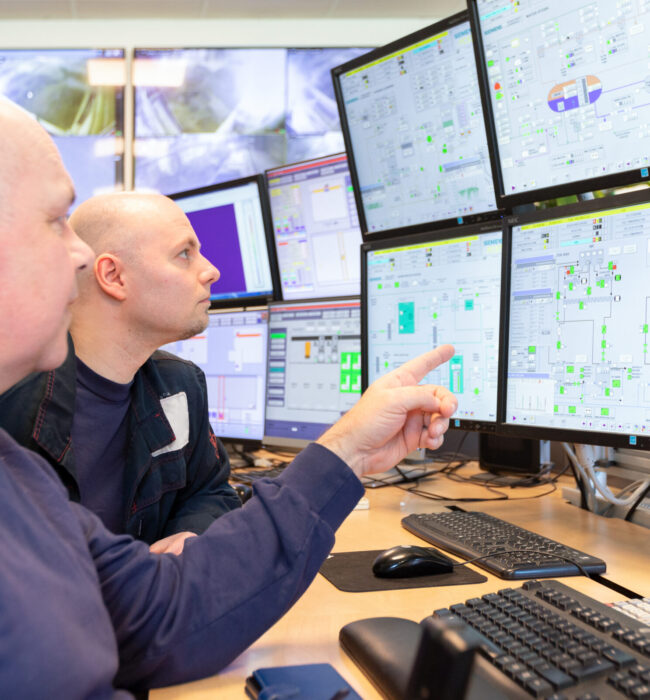
The control room - the nerve centre of the installation
In our control room, the entire process is closely monitored 24 hours a day, 7 days a week. This is done with the use of many computer screens and camera images, on which operator can see exactly what is happening on the premises and in the factory. Failures are spotted immediately so that they can be corrected quickly. Special computers keep track of the temperature of the incinerator, the supply of poultry manure and the emissions. The work permits are also issued in the control room.
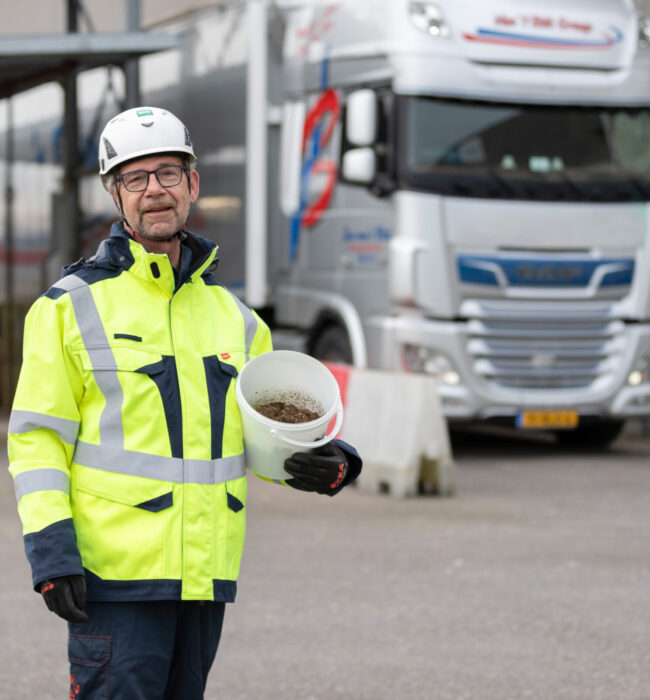
Lorries full of poultry manure
BMC Moerdijk processes one third of all poultry manure in the Netherlands. Every weekday, 60 to 70 lorries bring the poultry manure from all over the Netherlands to BMC Moerdijk. Upon arrival, the lorry is first weighed. The cargo is then inspected and our unloading operator takes a sample. The energy value of this sample is determined immediately. After approval, the driver may proceed with their vehicle to the unloading hall to unload the poultry manure. Before the lorry leaves our premises, it passes over the weighbridge and through our disinfection lane once more. In this way, we prevent the spread of animal diseases to the best degree we can. After this, the driver can be on their way again to collect a new load of poultry manure for BMC Moerdijk!
Storage of poultry manure
There are two large storage facilities for poultry manure on our site. In these storage facilities, all delivered loads of poultry manure are mixed well, so that a homogeneous fuel is created. This is important, because it allows for a stable combustion process. The poultry manure is mixed with grabs, which are so big that a passenger car can easily fit in them! The desired amount of poultry manure is dosed from the poultry manure storage facilities onto a conveyor belt, which transports the poultry manure to the boiler. Per hour, this amounts to about 55 tonnes. Before the poultry manure reaches the boiler, oversized pieces and metals are removed.
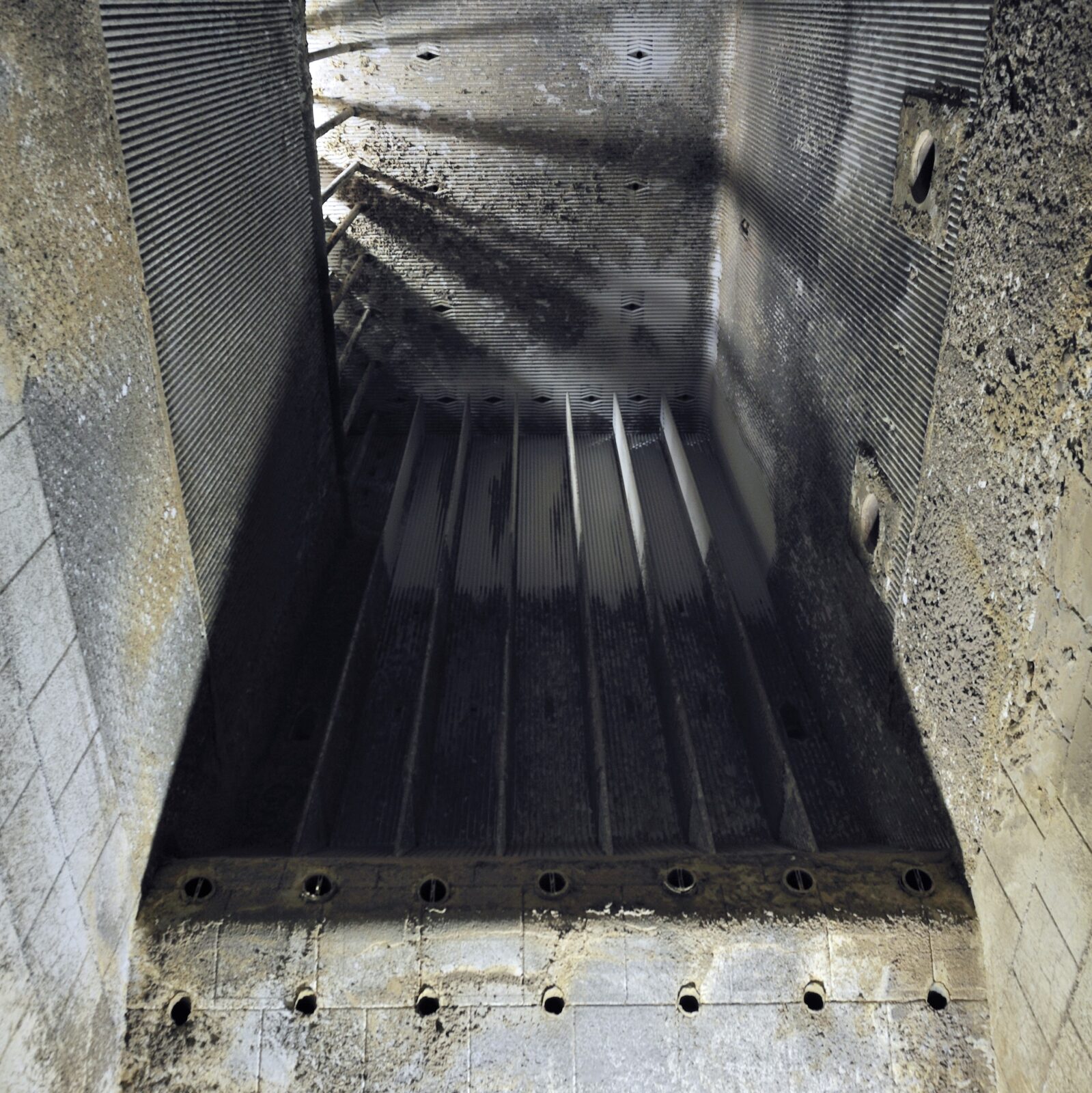
Fluidised bed furnace
The incineration process begins when the poultry manure is deposited into our fluidised bed furnace. Here, hot air is blown through a layer of sand at a temperature of 750°C. The sand behaves like a boiling liquid. The resulting flue gases are then post-combusted by adding supplementary air. This results in the temperature rising to more than 1000°C.
Steam turbine and generator
The heat generated in the boiler is used to heat the water in the steam boiler. The water evaporates and turns into steam. This steam ultimately leaves the boiler at a pressure of 65 bar and has a temperature of 482°C. This steam is used to power a steam turbine. To use all the energy from the steam boiler, several rows of blades are placed one after the other on the axis of the turbine. As the steam passes through the rows of blades, the steam pressure and temperature drop. This increases the volume of the steam, which is why the size of the blades is larger towards the back. The turbine rotates continuously at 3.000 revolutions per minute and is linked to a generator, which generates a voltage of 10.500 volts. Think of it as a large bicycle dynamo. This generates 36.5 MWh per hour, which amounts to 290.000.000 kWh of green electricity on an annual basis. We use about 15% of this ourselves.
When the steam leaves the turbine, the steam pressure is only 50 mbar and the temperature 36°C. The steam is further cooled in a condenser so that it is converted back to water, or condensate. This water then flows back into the boiler and so the circle is complete.
Our plant produces 132 tonnes of steam every hour, which is used to generate electricity. The used steam is converted back into water, after which it is made into steam again through heating. In other words, it’s a circular process!
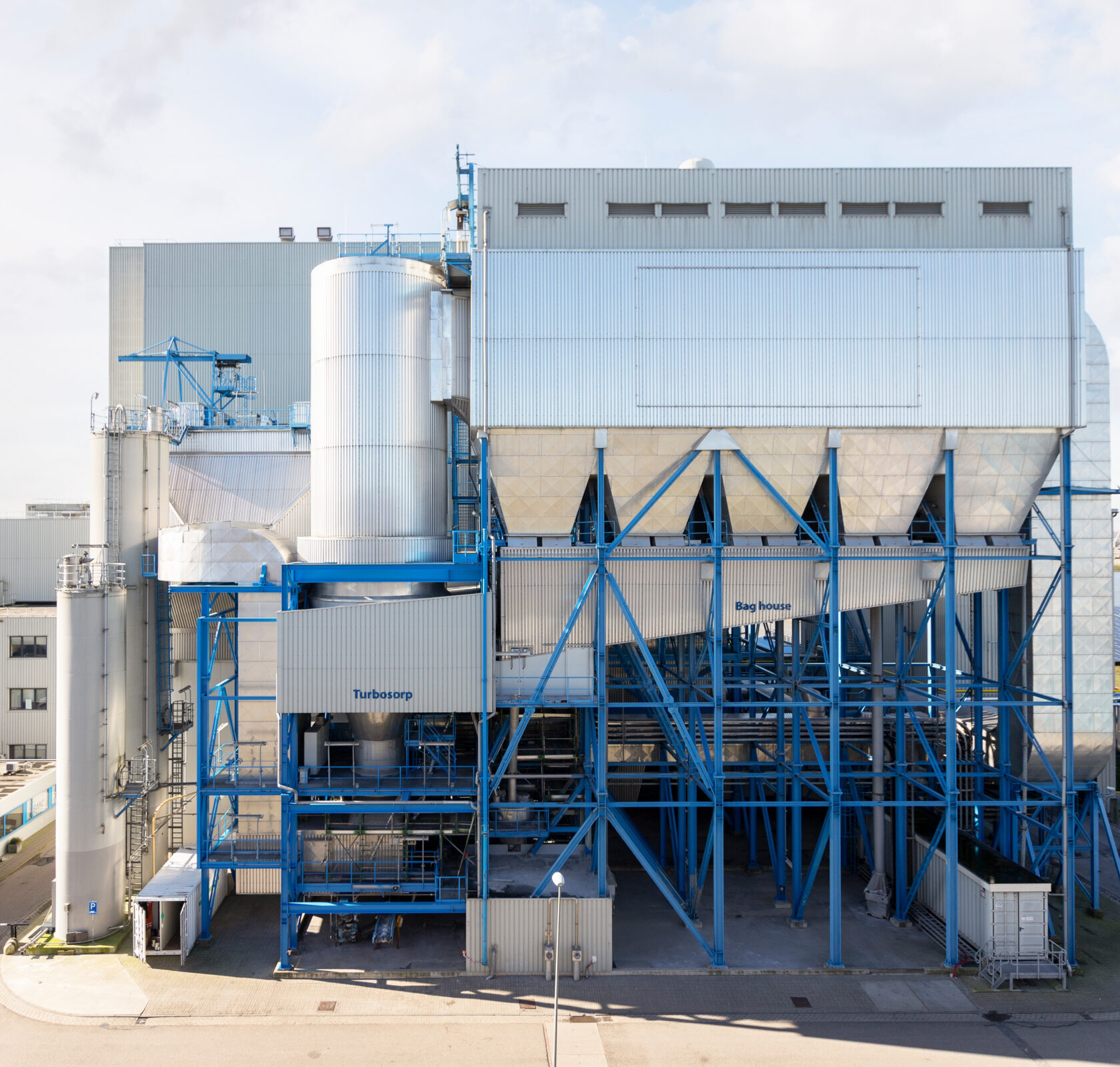
Gas scrubbing
The flue gases have given off most of their heat in the boiler and are still at a temperature of around 185°C. Now they go through a flue gas purification system. This is important, because our flue gases must comply with the strictest standards and must be clean before leaving the chimney. To monitor this, the emissions in the chimney are measured continuously. A very large fan, called lD-fan, ensures that the entire installation is under pressure so that flue gases cannot escape. There are two heat exchangers in the flue gas scrubbing system. The first transfers the heat from the flue gases leaving the ‘deNOx installation’ (NOx reduction installation) to the gases entering the deNOx installation. This reduces gas emissions by a significant amount. The second heat exchanger is located just in front of the chimney; here, we extract heat from the flue gases for reuse in our process.
The flue gases are scrubbed in three steps:
- The flue gases first pass through the electrostatic filter. Here, more than 95% of the matter present is removed from the flue gases by means of an electric charge.
- The next step is the Turbosorp®/cloth filter combination. In the Turbosorp®, lime is added to convert acidic components such as chlorine and sulphur into salts. The cloth filter is a second filter for dust and ashes. It is a type of large vacuum cleaner with 2.500 cloths. When the flue gases pass through the cloths, the dust remains on the cloths.
- Lastly, the flue gases pass through the deNOx installation (SNCR). Here, they are heated slightly and misted with ammonia. In a catalytic converter, the nitrogen oxides react with the ammonia and are converted to harmless nitrogen (N₂) and water.
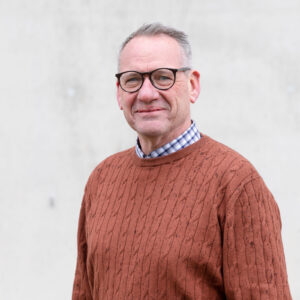
Would you like to know more?
We would be happy to answer all your technical questions!